The Best Motion Hardware for Reducing Risk
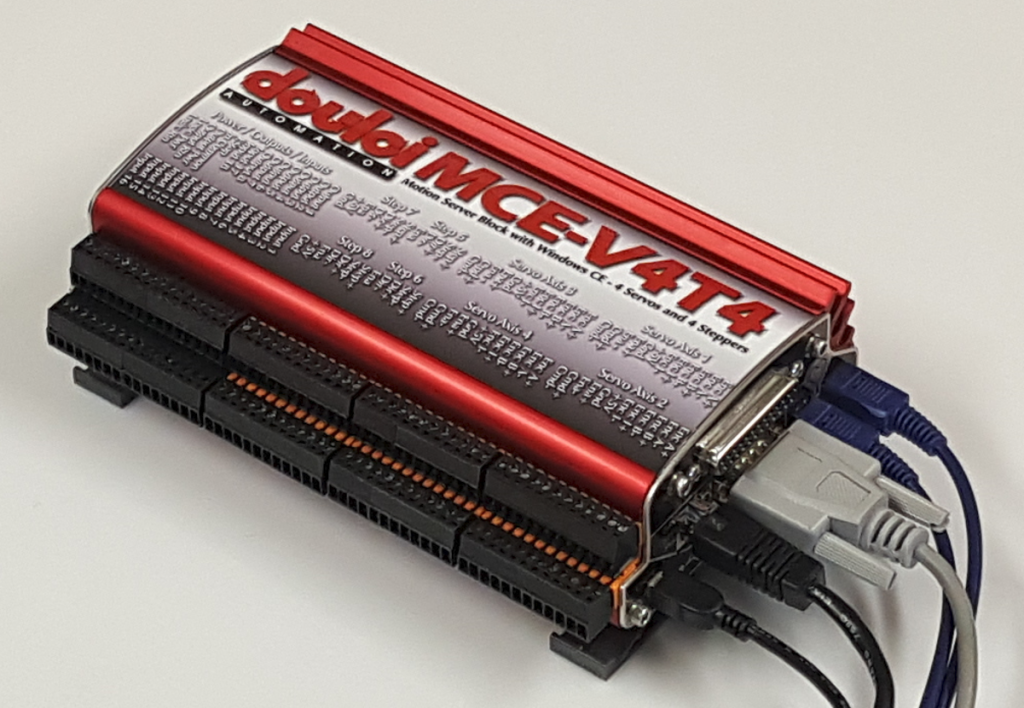
Motion System
- Controller can be ordered in configurations from 2 to 16 axes with mixed motor types
- Axes can be organized in multiple concurrent axis groups for flexible configuration
- Multiple controllers can communicate in star and ring configurations using RS232, RS485, or Fiber
- Velocity profiles include native trapezoidal and application-level s-curve and custom shapes
- Samples rates 500 Hz to 8 kHz providing high performance
- Native Interpolation Modes include linear, circular, helical, and curves composed of concatenated lines and arcs
- Application level Interpolation can be described in resident programs and run at the sample rate
- Coordination Modes include electronic gearing, camming, tangent, encoder-replaces-time, kinematics, motion superposition, and coordination tailoring
- High speed position capture supports high speed registration
- High speed position compare supports on-the-fly output operations in relationship to motion
Mixed Motor and Encoder Types
- Signal support for analog servo, digital servo, stepper motors
- Step rates and encoder count rates to 2 MHz
- Stepper Drive support through option slot for 1,2,3, or 4 internal microstepping drives
- Quadrature and BiSS encoder support
Onboard Language
- Graphical Block Interface or Text Programming Interface
- Programs cross-compile to native object code for very high performance
- Data structures and object oriented design support
- 64 concurrent tasks supported each running every controller sample
IO System
- (18) Isolated Digital Inputs, 5-24 volts
- (8) 2 amp 24 volt sourcing outputs with recirculating diodes for inductive loads
- (48) TTL IO points configurable as inputs or outputs on an individual bit basis. Compatible with Opto22 series D racks
- Optical Isolation between controller logic power, 24 volt inputs, 24 volt outputs, servo command signals, and servo enables
- Dual digital and analog watchdog safety systems suppresses motion signals at the hardware level in the event of a software failures, firmware failure, or dedicated EStop event
- (8) analog inputs on TTL inputs 1 through 8 for signals in the 0V-5V range
Processor
- 800 Mhz x86 processor
- 80 bit floating point hardware supporting transcendentals for kinematic applications
Command Signals
- Differential drivers for step/direction signals
- Differential receivers for encoders
- Optically isolated servo enable signals can source or sink
- Stepper enable provides open collector to ground
Communication
- USB connects Servo Application Workbench software to provide development and run-time view of controller during operation
- Ethernet server port provides host connection access for industrial HMI or network
- (2) RS232 ports
- (2) RS485 ports
- Fiber interface supports ring topology for inter-controller communication
Option Slot
- Additional RS232 ports
- Additional Axes
- Internal Drives
- Additional analog inputs and outputs
Enclosure
- Sturdy extruded aluminum enclosure suitable for an industrial environment
- DIN rail mounting feet
- Detachable 3.5mm screw terminal connectors supports field swap without rewiring
- Passive heat sink fins manage heat without active fan that can wear out
- 7.75″ x 4.75″ x 2.75″